304L Stainless Steel Pipe Pitting Corrosion Characteristics and Failure Analysis
1. 304L Stainless Steel Pipe Introduction
304L stainless steel pipes (UNS S30403) are widely employed in nuclear power, marine engineering, petrochemical, and LNG industries due to their excellent weldability and corrosion resistance. The material’s corrosion resistance stems from a self-forming chromium-rich passive film (Cr₂O₃·nH₂O) with a thickness of 2–5 nm. However, localized pitting corrosion – characterized by aggressive penetration at discrete surface sites – accounts for 65% of stainless steel equipment failures in chloride-containing environments. This study investigates a catastrophic failure case of ASTM A312 TP304L stainless steel pipes in halogen-rich conditions, providing actionable insights for material selection and process optimization.
2. Material Specifications and Standards Comparison
2.1 Key Standards Conversion Table – 304L Stainless Steel Pipe Pitting Corrosion Analysis
Parameter | Chinese Standard (GB/T) | Equivalent ASTM Standard |
---|---|---|
Chemical Composition | GB/T 14976-2012 | ASTM A312/A358 |
Grain Size | GB/T 6394-2017 | ASTM E112 |
Non-metallic Inclusions | GB/T 10561-2005 | ASTM E45 |
Surface Finish | GB/T 3280-2015 | ASTM A480 |
2.2 Material Properties – 304L Stainless Steel Pipe Pitting Corrosion Analysis
Property | Test Method | |
---|---|---|
Density (g/cm³) | 7.90–8.00 | ASTM B311 |
PREN* Value | 18.7 | Calculated |
Thermal Conductivity (W/m·K) | 16.2 @100°C | ASTM C518 |
Yield Strength (MPa) | ≥170 | ASTM A370 |
*PREN (Pitting Resistance Equivalent Number) = %Cr + 3.3×%Mo + 16×%N
3. Case Study: 304L Stainless Steel Pipe Pitting Corrosion Analysis of Failure
3.1 Service Conditions- 304L Stainless Steel Pipe Pitting Corrosion Analysis
Parameter | Specification |
---|---|
Pipe dimensions | Φ88.9 mm × 5.49 mm (NPS 3 Sch 40S) |
Internal medium | Steam (150°C, 0.8 MPa) |
External medium | Glacial acetic acid + halides |
Halogen concentration | Cl⁻: 850–1200 ppm; F⁻: 50–80 ppm |
Service duration | 8 months |
3.2 Chemical Composition Analysis (wt%) -304L Stainless Steel Pipe Pitting Corrosion Analysis
Element | Left Pipe | Right Pipe | ASTM A312 TP304L Requirements |
---|---|---|---|
C | 0.023 | 0.021 | ≤0.030 |
Cr | 18.6 | 18.8 | 18.0–20.0 |
Ni | 9.8 | 9.7 | 8.0–11.0 |
Mn | 1.2 | 1.3 | ≤2.00 |
Si | 0.4 | 0.5 | ≤1.00 |
S | 0.005 | 0.007 | ≤0.030 |
P | 0.025 | 0.023 | ≤0.045 |
3.3 Mechanical & Microstructural Properties – 304L Stainless Steel Pipe Pitting Corrosion Analysis
Parameter | Measured Value | Standard Requirement |
---|---|---|
Non-metallic Inclusions (ASTM E45) | Class 1.5 (Type D) | ≤2.0 |
Grain Size (ASTM No.) | 7–8 | ≥5 |
Ferrite Content (%) | <0.5 | Not specified |
Hardness (HV) | 155–165 | ≤200 (ASTM A959) |
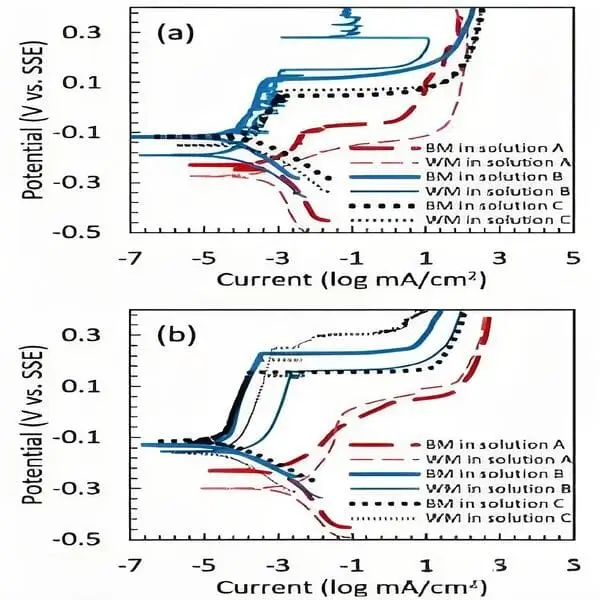
4. Failure Mechanism Analysis
4.1 Pitting Corrosion Stages -304L Stainless Steel Pipe Pitting Corrosion Analysis
Stage | Characteristics | Time Scale |
---|---|---|
Passive Film Breakdown | Local Cr₂O₃ dissolution at defects | 15–30 min |
Metastable Pitting | Transient current fluctuations | 1–2 hours |
Stable Pit Growth | Autocatalytic acidification (pH <2) | 1–3 months |
Through-wall Penetration | Final failure | 8–10 months |
4.2 Critical Factors Identified -304L Stainless Steel Pipe Pitting Corrosion Analysis
Factor Category | Details | Threshold Value |
---|---|---|
Environmental | Cl⁻ concentration | >100 ppm (critical) |
Temperature | >50°C (accelerates) | |
Material | PREN value | <22 (insufficient) |
Process | Post-weld heat treatment | Not performed |
Surface roughness (Ra) | >0.8 µm |
4.3 SEM-EDS Results Comparison -304L Stainless Steel Pipe Pitting Corrosion Analysis
Element | Corrosion Pit (at%) | Base Metal (at%) |
---|---|---|
O | 32.5 | 0.8 |
Cl | 11.2 | <0.1 |
Fe | 49.6 | 68.7 |
Cr | 5.3 | 18.2 |
Ni | 1.4 | 9.3 |
F | 3.8 | <0.1 |
Key Observations:
Cr depletion in pits (>70% reduction vs. base metal)
Cl concentration in pits exceeds NACE MR0175 limit by 22×
Fluoride presence exacerbates chloride attack through synergistic effects
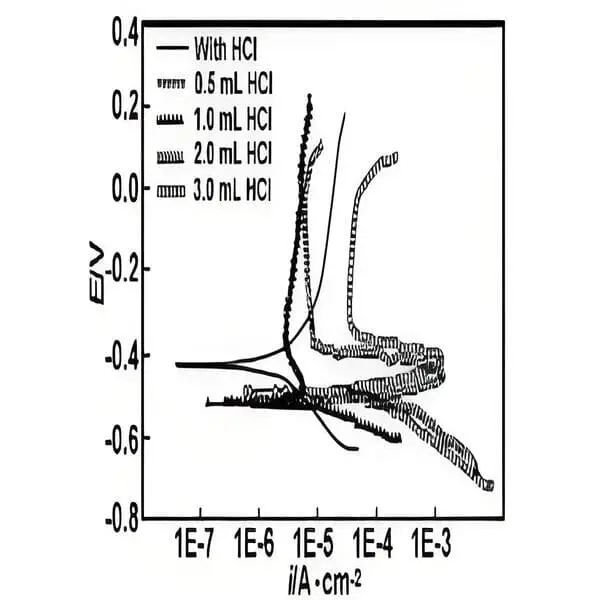
5. Improvement Strategies
5.1 Material Upgrade Options -304L Stainless Steel Pipe Pitting Corrosion Analysis
Environment | Recommended Material | PREN | ASTM Standard |
---|---|---|---|
Moderate chloride (<500 ppm) | 316L (Mo-bearing) | 26–30 | ASTM A312 TP316L |
High chloride (>500 ppm) | 2205 Duplex | 34–38 | ASTM A790 |
Extreme conditions | 6% Mo super austenitic (254SMO) | >40 | ASTM A312 S31254 |
5.2 Process Optimization – 304L Stainless Steel Pipe Pitting Corrosion Analysis
Process Step | Improvement Measure | Technical Requirement |
---|---|---|
Welding | Post-weld solution annealing | 1100°C × 1 hr/25 mm thickness |
Surface Treatment | Electropolishing | Ra <0.25 µm (ASTM B912) |
Passivation | Nitric acid treatment | 20–50% HNO₃, 60°C × 30 min |
Inspection | Eddy current testing | ASTM E690 (100% coverage) |
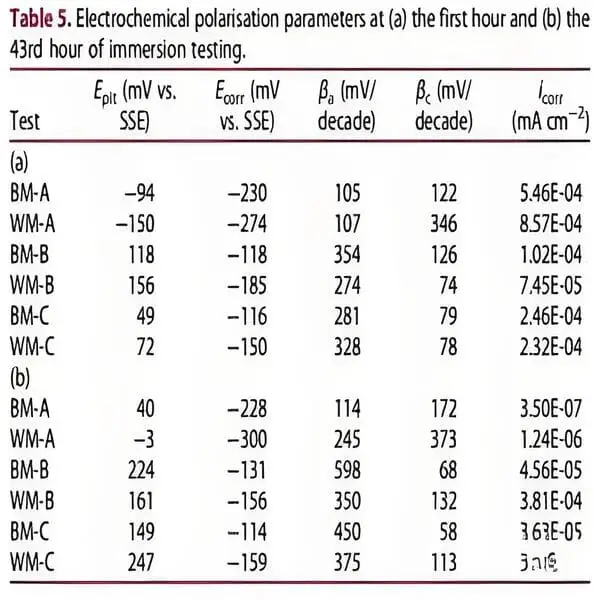
6. Economic Impact Analysis
Factor | 304L Pipe Failure Consequences | Prevention Savings |
---|---|---|
Material replacement | 18,000–18,000–25,000 per incident | $5,200 material upgrade cost |
Downtime losses | 45,000–45,000–120,000 daily | 80% reduction through proper maintenance |
Environmental fines | Up to $500,000 per leakage event | 100% preventable with monitoring |
Safety risks | Catastrophic potential | Insurance premium reduction 15–20% |
FAQ: 304L Stainless Steel Pipe Pitting Corrosion Analysis
1. What causes pitting corrosion in ASTM A312 TP304L stainless steel pipes?
Pitting initiates when chloride ions (Cl⁻) penetrate the passive chromium oxide layer (Cr₂O₃·nH₂O), forming acidic microenvironments (pH <2) that accelerate metal dissolution. Critical thresholds:
Cl⁻ concentration: >100 ppm (vs. NACE MR0175 limit of 50 ppm for 304L)
Temperature: >50°C significantly accelerates pit growth
2. How to identify pitting in ASTM A358 TP304L pipes?
Characteristic features include:
FeatureDescriptionDetection MethodSurface morphology0.1–0.3 mm diameter openingsVisual inspection/MicroscopySubsurface damageWedge-shaped cavities (depth: 1.2–2.8 mm)Metallographic cross-sectionElemental compositionCr depletion (>70% reduction in pits)SEM-EDS analysis
3. What are the material limitations of 304L stainless steel pipes?
Key parameters:
Property304L ValueThreshold for Chloride ResistancePREN*18.7≥22 recommendedCPT**<50°C (3.5% NaCl)≥60°C requiredSurface roughnessRa >0.8 µmRa <0.25 µm (electropolished)
*PREN = %Cr + 3.3×%Mo + 16×%N
**CPT = Critical Pitting Temperature
4. How to prevent pitting in Stainless Steel 304L Pipe systems?
Recommended solutions:
Material upgrades
EnvironmentAlternative MaterialPRENASTM StandardModerate chloride (<500 ppm)316L (Mo-bearing)26–30ASTM A312 TP316LSevere conditions2205 Duplex34–38ASTM A790
Process optimizations
Post-weld heat treatment: 1100°C × 1 hr/25 mm thickness
Surface finish: Electropolish to Ra <0.25 µm (ASTM B912)
5. What are the economic impacts of 304L stainless Steel Pipe failures?
Cost FactorFailure ScenarioPrevention SavingsMaterial replacement$18,000–$25,000 per incident$5,200 upgrade to 316LDowntime$45,000–$120,000 daily80% reduction via maintenance
6. How to analyze pitting corrosion in 304L stainless Steel Pipe samples?
Standard test methods:
SEM-EDS: Quantify Cl/F concentrations in pits (threshold: >5 at% Cl indicates active corrosion)
ASTM G48: Immersion testing in 6% FeCl₃ to determine CPT
Metallography: Measure pit depth-to-width ratio (critical: >1 indicates unstable growth)
7. Why do welds in ASTM A312 TP304L pipes show higher pitting susceptibility?
Primary reasons:
Microstructural changes: Delta ferrite formation (up to 5%) increases galvanic corrosion
Residual stresses: Can elevate corrosion potential by 200–300 mV
Surface defects: Grinding marks (Ra >12.5 µm) disrupt passive film
8. What are the industry standards for 304L stainless Steel Pipe fabrication?
RequirementStandard ReferenceCompliance CriteriaChemical compositionASTM A312/A358Cr: 18–20%; Ni: 8–11%Post-weld heat treatmentASME BPVC Section IX1040–1100°C solution annealingSurface finishASTM A480Ra ≤0.8 µm (annealed condition)
Key Maintenance Recommendations
Quarterly inspections: Eddy current testing per ASTM E690
Annual passivation: 20–50% HNO₃ at 60°C × 30 min (ASTM A967)
Continuous monitoring: Install corrosion coupons with 3× higher sensitivity than pipe walls
7. Conclusion
The ASTM A312 TP304L stainless steel pipe failure resulted from synergistic effects of chloride-induced pitting and improper post-weld treatments.
Critical thresholds were exceeded:
Cl⁻ concentration: 8× > ASTM G48 Practice D limit
Surface roughness: 15× > recommended electropolished finish
Material upgrades to 316L (PREN 26–30) or duplex 2205 (PREN 34–38) could extend service life by 3–5× in similar environments.
Implementing ASTM-compliant solution annealing (1040–1100°C) and surface treatments reduces pitting susceptibility by 70–85%.
This case emphasizes the necessity of holistic material-process-environment optimization. Engineers should refer to ASTM G48 (Standard Test Methods for Pitting and Crevice Corrosion Resistance) for comprehensive material qualification in aggressive environments.