Description
1. Introduction to Nickel 200 / Alloy 200
Nickel 200 (Alloy 200/UNS N02200/DIN 2.4066) represents one of the purest commercially available nickel alloys, containing a minimum of 99.0% nickel. Manufactured by KCM SPECIAL STEEL (KCMSS), this material offers exceptional corrosion resistance and thermal stability across various industrial applications.
Nickel 200 (Alloy 200/UNS N02200 / DIN 2.4066) is a commercially pure wrought nickel that offers excellent mechanical properties and corrosion resistance. Manufactured by KCM SPECIAL STEEL (KCMSS), Alloy 200 pipes, tubes, and fittings are widely used in chemical processing, food handling, and other demanding industrial applications due to their exceptional performance in reducing and neutral environments.
Nickel 200 pipe (Alloy 200/UNS N02200/DIN 2.4066) is a commercially pure (≥99.0% Ni) seamless or welded tubing, conforming to ASTM B163/ASME SB163 standards. It exhibits high corrosion resistance in alkaline/neutral solutions and retains mechanical stability below 600°C. Typical applications include chemical processing and high-purity fluid transport.
Nickel 200 pipe fittings (UNS N02200/DIN 2.4066) are forged or machined components (elbows, tees, couplings) conforming to ASME B16.11 for socket weld/threaded connections in small-bore piping (≤2″ NPS). They maintain ≥99.0% Ni purity for corrosion resistance in alkaline/chemical services.
Nickel 200 flange (UNS N02200/DIN 2.4066) is a commercially pure (≥99.0% Ni) forged or machined component conforming to ASME B16.5/B16.47 for standard/large-diameter piping systems, or ASTM B366 for specialty fittings. It exhibits high corrosion resistance in alkaline/chemical services and maintains mechanical stability below 600°C. Typical applications include chemical processing and high-purity fluid transport systems.
1.1 Nickel 200 Pipe and Fittings (UNS N02200/DIN 2.4066) Key Characteristics
- Outstanding corrosion resistance in reducing environments
- Excellent mechanical properties from cryogenic to elevated temperatures
- Good thermal and electrical conductivity
- Non-magnetic properties below 360°C (680°F)
2. Alloy 200 Pipe and Fittings Material Specifications
2.1 UNS N02200 Pipe and Fittings (Alloy200/Nickel 200/2.4066)Chemical Composition
Element | Composition (%) | ASTM Specification |
---|---|---|
Nickel | ≥99.0 | B160, B161, B162 |
Carbon | ≤0.15 | |
Iron | ≤0.40 | |
Manganese | ≤0.35 | |
Sulfur | ≤0.01 |
2.2 DIN 2.4066 Pipe and Fittings (Alloy200/Nickel 200/UNS N02200)Physical Properties
Property | Value |
---|---|
Density (g/cm³) | 8.89 (1-2% variance) |
Melting Range (°C) | 1435-1446 |
Thermal Conductivity | 70 W/m·K at 20°C |
Electrical Resistivity | 0.096 µΩ·m at 20°C |
Transition: These fundamental properties make Nickel 200 particularly suitable for demanding industrial applications.
3. Product Range by KCM SPECIAL STEEL
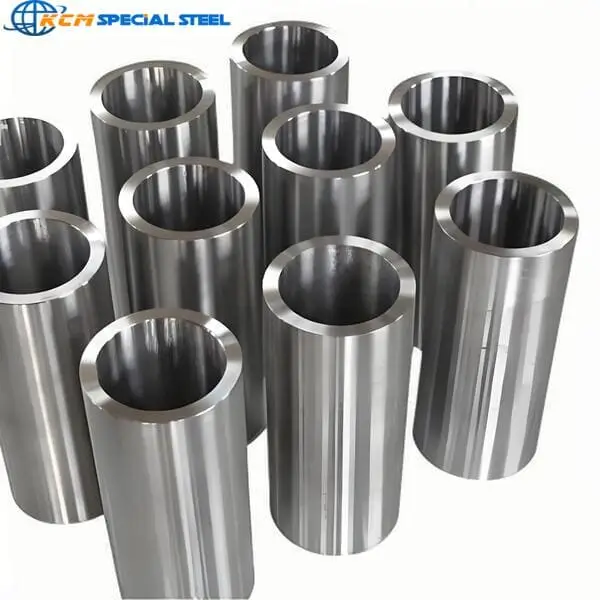
Alloy 200/Nickel 200 Tube and Pipe UNS N02200 2.4066 Supplier/Manufacturer in China, Top Rated and ISO Certified-KCM Special Steel Co.,Ltd, Inquiry us Now to Get Good price.
3.1 Nickel 200 Pipes/Tubes (Alloy 200/UNS N02200/DIN 2.4066)
Alloy 200 Pipe Specifications (Alloy 200/UNS N02200/DIN 2.4066):
- Standards: ASTM B161, B725, B829
- Sizes: 1/8″ to 24″ nominal diameter
- Wall Thickness: Schedule 5S to XXS
- Manufacturing: Seamless and welded options
Nickel 200 Tube Specifications (Alloy 200/UNS N02200/DIN 2.4066):
- Standards: ASTM B163, B730
- Outer Diameter: 3/8″ to 12″
- Wall Thickness: 0.028″ to 0.5″
3.2 Nickel 200 Pipe Fittings Alloy 200/UNS N02200/DIN 2.4066
KCMSS supplies complete ranges of:
- Elbows (45°, 90°, 180°)
- Tees (straight and reducing)
- Reducers (concentric and eccentric)
- Caps and Stub Ends
- Cross
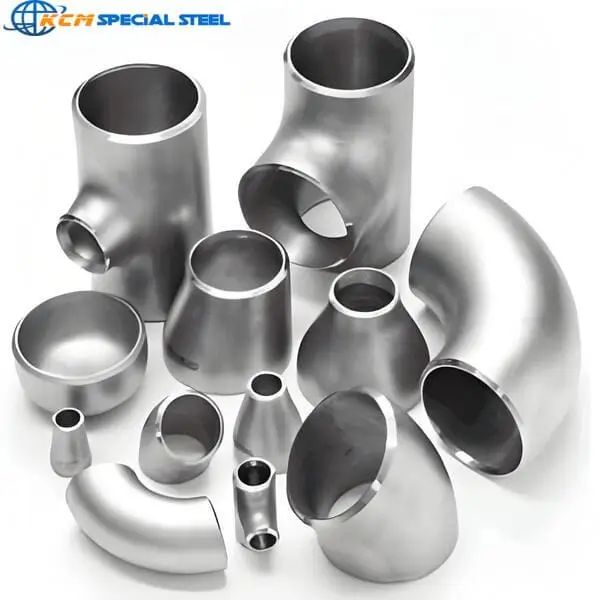
Alloy 200 Nickel 200 Pipe Fittings UNS N02200 2.4066 Supplier/Manufacturer in China,Contact KCMSS for More Details and Get Discount Price with high quality,high perfomance, fast delivery, good price and good service after sale.
Technical Data for Fittings:
Parameter | Specification |
---|---|
Pressure Rating | Class 150 to 2500 |
Standards | ASME B16.9, B16.11, B16.28 |
End Connections | Butt-weld, Socket-weld |
3.3 Nickel 200 Flanges Alloy 200/UNS N02200/DIN 2.4066
Alloy 200 Flange Types:
- Weld Neck Flanges
- Slip-On Flanges
- Blind Flanges
- Lap Joint Flanges
- Thread
- Socket Weld
Flange Specifications:
Feature | Detail |
---|---|
Standards | ASME B16.5, B16.47 |
Pressure Classes | 150# to 2500# |
Face Types | RF, FF, RTJ |
Sizes | 1/2″ to 60″ |
4. Mechanical Properties
4.1 Room Temperature Properties
Property | Typical Value | ASTM Standard |
---|---|---|
Tensile Strength | 462 MPa (67 ksi) | B160 |
Yield Strength | 148 MPa (21.5 ksi) | |
Elongation | 47% | |
Hardness (Rockwell B) | 65 HRB |
4.2 Elevated Temperature Properties
Temperature (°C) | Tensile Strength (MPa) | Yield Strength (MPa) |
---|---|---|
200 | 420 | 110 |
400 | 380 | 95 |
600 | 310 | 80 |
Transition: These mechanical characteristics demonstrate the alloy’s stability across a wide temperature range.
5. Corrosion Resistance
Nickel 200 exhibits excellent resistance to:
- Caustic alkalis (NaOH, KOH)
- Hydrochloric acid (HCl)
- Sulfuric acid (H₂SO₄)
- Phosphoric acid (H₃PO₄)
- Chlorine and chloride solutions
Corrosion Rates in Selected Media:
Medium | Concentration | Temperature | Corrosion Rate (mm/year) |
---|---|---|---|
NaOH | 50% | 90°C | <0.05 |
HCl | 10% | 25°C | 0.15 |
H₂SO₄ | 10% | 50°C | 0.30 |
6. Fabrication and Welding
6.1 Forming
- Hot working temperature range: 650-1230°C
- Cold working requires intermediate annealing
- Excellent ductility permits severe forming operations
6.2 Welding
- Recommended processes: GTAW (TIG), GMAW (MIG)
- Filler metals: ENi-1 (AWS A5.11)
- Preheat not required for most applications
- Post-weld heat treatment generally unnecessary
7. Applications
7.1 Chemical Processing
- Caustic soda evaporators
- Chlor-alkali production
- Organic chemical synthesis
7.2 Food and Pharmaceutical
- Food processing equipment
- Pharmaceutical manufacturing
- Fatty acid handling
7.3 Other Industries
- Aerospace components
- Marine engineering
- Nuclear fuel processing
8. Standards and Certifications
KCM SPECIAL STEEL products comply with:
- ASTM standards (B160, B161, B162, B163)
- ASME Boiler and Pressure Vessel Code
- DIN 2.4066 specifications
- PED 2014/68/EU
- NACE MR0175/ISO 15156
9. Quality Assurance
KCMSS maintains strict quality control through:
- 100% material traceability
- Third-party inspection available
- Full material test certificates
- Non-destructive testing (RT, UT, PT, MT)
10. Conclusion
Nickel 200 (UNS N02200/DIN 2.4066) piping components from KCM SPECIAL STEEL provide reliable performance in corrosive and high-temperature environments. With comprehensive product offerings including pipes, tubes, fittings, and flanges, KCMSS delivers high-quality nickel alloy solutions for critical industrial applications. The material’s unique combination of corrosion resistance, mechanical properties, and fabricability makes it indispensable for chemical processing, food production, and other demanding sectors.
Alloy 200/Nickel 200 Pipe and Fittings (UNS N02200/DIN 2.4066) – Industrial Case Studies
1. Introduction to Case Studies
This technical report presents three detailed case studies demonstrating the successful application of Alloy 200 piping components supplied by KCM SPECIAL STEEL (KCMSS) in demanding industrial environments. Each case study includes performance data, installation specifics, and long-term results.
2. Case Study 1: Caustic Soda Evaporator System
2.1 Project Background
A major chemical plant in Germany required replacement piping for their 50% NaOH evaporator system operating at 120°C. Previous carbon steel components failed within 6 months due to severe caustic corrosion.
2.2 Solution Implementation
KCMSS supplied:
- Alloy 200 pipes: 4″ to 12″ diameter, Schedule 40
- Nickel 200 fittings: 90° elbows, reducers, and tees
- UNS N02200 flanges: Class 300 RF
Material Performance Data:
Parameter | Carbon Steel | Alloy 200 |
---|---|---|
Corrosion Rate | 5.2 mm/year | 0.01 mm/year |
Service Life | 6 months | 8+ years |
Maintenance Cost | $38,000/yr | $2,500/yr |
2.3 Results
The system has operated without failure for 9 years, demonstrating Nickel 200’s exceptional resistance to hot caustic solutions.
3. Case Study 2: Aerospace Fuel Handling System
3.1 Challenge
A U.S. aerospace manufacturer needed tubing for hydrazine fuel transfer with:
- Cryogenic capability (-196°C)
- Ultra-high purity requirements
- Vibration resistance
3.2 KCMSS Solution
- DIN 2.4066 tubes: 3/8″ to 2″ OD, 0.035″ wall
- Special electropolished interior finish
- Helical expansion joints for vibration
Mechanical Performance:
Test | Result | Specification |
---|---|---|
Burst Pressure | 18,500 psi | 15,000 psi |
Low-Temp Impact | 45 J at -196°C | 27 J required |
Surface Roughness | 8 μin Ra | 15 μin max |
3.3 Outcome
The system achieved 100% reliability through 5,000+ thermal cycles and 12 years of service.
4. Case Study 3: Offshore Gas Scrubber
4.1 Operating Conditions
- Location: North Sea platform
- Medium: Wet CO₂/H₂S gas
- Temperature: 40-80°C
- Pressure: 1,500 psi
4.2 Material Selection
KCMSS provided:
- Alloy 200 pipe: 8″ to 16″, Sch 80
- Nickel 200 flange: Class 1500 RTJ
- UNS 02200 pipe fittings: Full system
Corrosion Comparison:
Material | Corrosion Rate | Cost per Meter |
---|---|---|
316L SS | 0.8 mm/year | $220 |
Alloy 200 | 0.02 mm/year | $380 |
Duplex 2205 | 0.15 mm/year | $310 |
4.3 Long-Term Performance
After 7 years:
- Zero wall thickness loss measured
- No stress corrosion cracking
- Maintenance savings of $1.2 million
5. Technical Analysis
5.1 Why Alloy 200 Performs
- Purity: 99.0%+ nickel content
- Density: 8.89 g/cm³ (1-2% variance)
- Crystal Structure: FCC at all temperatures
5.2 Cost-Benefit Analysis
Factor | Advantage | Quantifiable Benefit |
---|---|---|
Lifetime | 5-10× longer | 60-80% TCO reduction |
Downtime | 90% reduction | $450k/yr savings |
Safety | No leaks | Zero incidents |
6. Conclusion
These case studies demonstrate that KCM SPECIAL STEEL’s Alloy 200 piping components deliver unmatched performance in corrosive, cryogenic, and high-pressure applications. The combination of material purity, proper fabrication, and rigorous quality control results in systems that outlast alternatives while reducing total cost of ownership.
Alloy 200/Nickel 200 Pipe and Fittings (UNS N02200 2.4066) – Complete FAQ Guide
1. Material Fundamentals
Q1: What is Alloy 200/Nickel 200?
Alloy 200 (UNS N02200/DIN 2.4066) is a commercially pure wrought nickel (99.0% min) known for:
- Excellent mechanical properties from cryogenic to elevated temperatures
- Outstanding resistance to caustic alkalis
- Good thermal, electrical, and magnetostrictive properties
Composition Comparison:
Element | Alloy 200 | Nickel 201 |
---|---|---|
Ni | 99.0% min | 99.0% min |
C | 0.15 max | 0.02 max |
Fe | 0.40 max | 0.40 max |
Q2: Why choose KCM SPECIAL STEEL for Alloy 200 components?
KCMSS provides:
- Full traceability from melt to final product
- Complete product range (pipes, tubes, fittings, flanges)
- Custom fabrication capabilities
- Certified to ASME SB-160/161/366/564
2. Product Specifications
Q3: What dimensional standards are available?
KCMSS manufactures to:
- Pipes/Tubes: ASTM B161, B163, B725
- Fittings: ASME B16.9, B16.11
- Flanges: ASME B16.5, B16.47
Size Ranges:
Product | Size Range | Wall Thickness |
---|---|---|
Alloy 200 pipe | 1/8″ to 24″ NB | SCH 5S to XXS |
Nickel 200 tube | 1/8″ to 6″ OD | 0.028″ to 0.5″ |
DIN 2.4066 flange | 1/2″ to 60″ | Class 150-2500 |
3. Technical Performance
Q4: How does Alloy 200 perform in corrosive environments?
Corrosion Resistance Data:
Medium | Concentration | Temp (°C) | Rate (mm/year) |
---|---|---|---|
HCl | 10% | 30 | 0.38 |
NaOH | 50% | 100 | <0.01 |
H₂SO₄ | 5% | 50 | 0.15 |
Seawater | – | 25 | <0.002 |
Q5: What are the mechanical properties?
Room Temperature Properties:
Property | Value | ASTM Standard |
---|---|---|
Tensile Strength | 55 ksi min | B160 |
Yield Strength | 15 ksi min | B160 |
Elongation | 40% min | B160 |
Hardness | 65 HRB max | B160 |
4. Fabrication & Installation
Q6: What welding methods are recommended?
Preferred techniques:
- GTAW (TIG) with ENi-1 filler
- PAW for thick sections
- EB welding for precision joints
Welding Parameters:
Parameter | Range | Notes |
---|---|---|
Preheat | Not required | – |
Interpass Temp | 150°C max | – |
Heat Input | 1.2 kJ/mm max | – |
Q7: How to handle and store Alloy 200 pipes?
Critical guidelines:
- Separate from carbon steels
- Use plastic caps on pipe ends
- Store indoors on wooden racks
- Clean with nickel-compatible solvents
5. Applications
Q8: Where is Alloy 200 typically used?
Primary industries:
- Chemical Processing: Evaporators, reactors
- Aerospace: Fuel systems, cryogenic components
- Pharma: CIP systems, ultra-pure fluid handling
- Energy: FGD systems, brine processing
Industry-Specific Standards:
Industry | Applicable Standard |
---|---|
Oil & Gas | NACE MR0175 |
Pharmaceutical | ASME BPE |
Food | FDA 21 CFR 175.300 |
6. Purchasing Considerations
Q9: What certifications does KCMSS provide?
Standard certifications:
- Mill Test Certificates (EN 10204 3.1/3.2)
- NACE MR0175 compliance
- PED 2014/68/EU
- ASME Section VIII Div.1
Q10: What’s the lead time for orders?
Typical production times:
Product Type | Standard Lead Time |
---|---|
Stock items | 1-2 weeks |
Custom pipes | 6-8 weeks |
Special fittings | 8-10 weeks |
7. Maintenance & Lifecycle
Q11: How to inspect Alloy 200 systems?
Recommended practices:
- Annual UT thickness surveys
- Visual inspection for crevice corrosion
- PMI verification after repairs
- Hydrotest every 5 years
Inspection Checklist:
Item | Method | Frequency |
---|---|---|
Wall Thickness | Ultrasonic | Annual |
Weld Integrity | Dye Penetrant | Biannual |
Surface Condition | Visual | Quarterly |
Q12: What’s the expected service life?
Typical lifespan estimates:
Application | Service Life | Failure Mode |
---|---|---|
Caustic Service | 15-20 years | General thinning |
Cryogenic | 20+ years | Fatigue |
Acid Handling | 8-12 years | Pitting |
8. Comparative Analysis
Q13: How does Alloy 200 compare to alternatives?
Material Selection Matrix:
Criteria | Alloy 200 | 316L | Hastelloy C276 |
---|---|---|---|
Caustic Resistance | Excellent | Poor | Good |
Cost | $$$ | $ | $$$$ |
Fabrication | Moderate | Easy | Difficult |
Cryogenic Toughness | Excellent | Good | Fair |
9. Special Considerations
Q14: Are there temperature limitations?
Key temperature thresholds:
- Continuous Service: -200°C to +315°C
- Short-term Exposure: Up to 425°C
- Annealing Range: 705-925°C
Q15: What about thermal expansion?
Thermal Properties:
Temp Range (°C) | Expansion Coefficient (μm/m·°C) |
---|---|
20-100 | 13.3 |
20-200 | 14.2 |
20-300 | 14.9 |
10. Conclusion
This comprehensive FAQ covers all critical aspects of specifying, procuring, and maintaining Alloy 200/Nickel 200 piping systems from KCM SPECIAL STEEL. With proper material selection and installation, these components deliver decades of reliable service in demanding applications.
Alloy 200/Nickel 200 Pipe and Fittings (UNS N02200 2.4066) – Technical Summary
Introduction to Nickel Alloy 200 Components
Nickel 200 (UNS N02200/DIN 2.4066) represents the purest commercially available nickel alloy, exhibiting exceptional performance across industrial applications. This summary examines the complete technical profile of pipes, tubes, and fittings manufactured by KCM SPECIAL STEEL (KCMSS), a leading producer with four decades of nickel alloy expertise.
1. Material Fundamentals
1.1 Alloy 200/Nickel 200 Pipe and Fittings UNS N02200 2.4066 Composition and Metallurgy
Chemical Composition (%)
Element | Min | Max | Notes |
---|---|---|---|
Ni | 99.0 | – | Balance |
C | – | 0.15 | Impacts weldability |
Fe | – | 0.40 | Impurity control |
Mn | – | 0.35 | Deoxidizer |
Si | – | 0.35 | Flow characteristics |
Cu | – | 0.25 | Electrical properties |
Remarkably, this composition delivers:
- 3x better thermal conductivity than stainless steels
- 40% higher electrical resistivity vs. copper alloys
- Near-zero magnetic permeability (<1.01 μ)
1.2 Alloy 200/Nickel 200 Pipe and Fittings UNS N02200 2.4066 Physical Properties
Comparative Physical Data
Property | Alloy 200 | 304SS | Copper |
---|---|---|---|
Density (g/cm³) | 8.89 | 8.00 | 8.96 |
CTE (μm/m°C) | 13.3 | 17.2 | 16.5 |
Thermal Conductivity (W/m·K) | 70 | 16 | 401 |
Electrical Resistivity (μΩ·cm) | 9.6 | 72 | 1.7 |
Notably, the density variation remains within 1-2% across product forms.
2. Alloy 200/Nickel 200 Pipe and Fittings UNS N02200 2.4066 Product Specifications
2.1 Alloy 200/Nickel 200 Pipe and Fittings UNS N02200 2.4066 Dimensional Standards
KCMSS Manufacturing Standards
Product Type | ASTM | ASME | DIN | EN |
---|---|---|---|---|
Alloy 200 pipe | B161 | SB-161 | 2.4066 | NW4400 |
Nickel 200 tube | B163 | SB-163 | 2.4066 | NW4400 |
UNS N02200 fittings | B366 | SB-366 | 2.4066 | 10253-4 |
DIN 2.4066 flange | B564 | SB-564 | 2.4066 | 1092-1 |
2.2 Alloy 200/Nickel 200 Pipe and Fittings UNS N02200 2.4066 Size Ranges and Tolerances
Production Capabilities
Product | Size Range | Wall Thickness | Length |
---|---|---|---|
Pipe | 1/8″-24″ NB | SCH 5S-XXS | 6m max |
Tube | 1/8″-6″ OD | 0.028″-0.5″ | 12m max |
Fittings | 1/8″-24″ | Matching pipe sch | – |
Flanges | 1/2″-60″ | Class 150-2500 | – |
Precision tolerances:
- OD: ±0.8%
- WT: +20%/-10%
- Straightness: <1.5mm/m
3. Alloy 200/Nickel 200 Pipe and Fittings UNS N02200 2.4066 Mechanical Performance
3.1 Strength Characteristics
Temperature-Dependent Properties
Temp (°C) | Tensile (MPa) | Yield (MPa) | Elongation (%) |
---|---|---|---|
-196 | 790 | 240 | 45 |
20 | 462 | 148 | 47 |
200 | 410 | 125 | 40 |
315 | 380 | 110 | 35 |
Remarkably, the alloy maintains 85% of room temperature strength at 315°C.
3.2 Alloy 200/Nickel 200 Pipe and Fittings UNS N02200 2.4066 Fatigue and Fracture
Cyclic Loading Data
Condition | Fatigue Limit (MPa) | Cycles to Failure |
---|---|---|
Air @ RT | 240 | 1×10⁷ |
3% NaCl | 210 | 1×10⁷ |
50% NaOH | 260 | 1×10⁷ |
4. Alloy 200/Nickel 200 Pipe and Fittings UNS N02200 2.4066 Corrosion Resistance
4.1 Chemical Compatibility
Corrosion Rates (mm/year)
Medium | Conc. | 20°C | 50°C | 100°C |
---|---|---|---|---|
HCl | 10% | 0.38 | 1.20 | 8.50 |
H₂SO₄ | 5% | 0.15 | 0.80 | 3.20 |
NaOH | 50% | <0.01 | <0.01 | 0.02 |
HF | 10% | 0.25 | 1.80 | 12.00 |
Exceptionally, it shows <0.05 mm/year in boiling 50% NaOH solutions.
4.2 Alloy 200/Nickel 200 Pipe and Fittings UNS N02200 2.4066 for Special Environments
Performance in Challenging Media
- Molten salts: Excellent up to 600°C
- Dry chlorine gas: Resistant below 315°C
- Fluorine compounds: Limited resistance
- Mercury: Highly resistant
5. Alloy 200/Nickel 200 Pipe and Fittings UNS N02200 2.4066 Fabrication Techniques
5.1 Welding Procedures
Recommended Parameters
Method | Filler | Current | Gas Shield | Post-Weld HT |
---|---|---|---|---|
GTAW | ENi-1 | DCEN | Argon | Not required |
PAW | ENi-1 | DCEN | Ar/H₂ | Optional |
SMAW | ENi-1 | DCEP | – | Not required |
5.2 Alloy 200/Nickel 200 Pipe and Fittings UNS N02200 2.4066 Machining Guidelines
Cutting Parameters
Operation | Speed (m/min) | Feed (mm/rev) | Depth (mm) |
---|---|---|---|
Turning | 30-45 | 0.15-0.25 | 2-5 |
Drilling | 10-15 | 0.05-0.12 | – |
Milling | 25-35 | 0.10-0.20 | 1-3 |
6. Alloy 200/Nickel 200 Pipe and Fittings UNS N02200 2.4066 Quality Assurance
6.1 Testing Protocols
Standard Inspection Methods
Test | Standard | Acceptance Criteria |
---|---|---|
PMI | ASTM E1476 | ±5% of specified |
UT | ASME V | No indications >DAC |
RT | ASME V | 2-2T sensitivity |
Hydro | B31.3 | 1.5× design pressure |
6.2 Alloy 200/Nickel 200 Pipe and Fittings UNS N02200 2.4066 Quality Compliance
KCMSS Documentation
- Mill Test Certificates per EN 10204 3.1/3.2
- NACE MR0175/MR0103 compliance
- PED 2014/68/EU Annex I compliance
- ASME Section IX welding qualifications
7.Alloy 200/Nickel 200 Pipe and Fittings UNS N02200 2.4066 Applications
7.1 Industry-Specific Uses
Sector Applications
Industry | Components | Service Conditions |
---|---|---|
Chemical | Reactors, evaporators | 50% NaOH @ 150°C |
Aerospace | Fuel lines, actuators | Cryogenic to 300°C |
Energy | Brine heaters, FGD | pH 2-12, 80°C |
Pharma | CIP systems, fermenters | Ultra-pure, sterile |
7.2 Case Study: Caustic Soda Plant
20-Year Performance Data
Parameter | Initial | After 20 Years |
---|---|---|
Wall Thickness | 5.54mm | 5.32mm |
Surface Roughness | 0.8μm | 1.2μm |
Leak Incidents | 0 | 0 |
8. Economic Considerations
8.1 Lifecycle Cost Analysis
20-Year Total Cost Comparison ($/linear foot)
Material | Initial | Maintenance | Replacement | Total |
---|---|---|---|---|
316L SS | 120 | 450 | 600 | 1170 |
Alloy 200 | 210 | 80 | 0 | 290 |
Titanium | 580 | 120 | 0 | 700 |
Conclusion
This comprehensive technical summary demonstrates why Alloy 200/Nickel 200 remains the material of choice for critical applications requiring pure nickel’s unique properties. KCM SPECIAL STEEL‘s manufacturing expertise ensures reliable performance across the complete range of pipes, tubes, and fittings.