Nickel Alloy Pipe Supplier in China / ISO Certified Manufacturer: KCM Special Steel Co., Ltd
KCM Special Steel Co., Ltd is a leading supplier and ISO-certified manufacturer of premium nickel alloy pipes in China. Renowned for its advanced production capabilities, strict adherence to global quality standards, and versatile product range, the company delivers solutions for industries requiring corrosion-resistant, high-temperature, and durable piping systems.
Nickel Alloy Hastelloy C-276 Pipe and Fittings UNS N10276 2.4819
Alloy 201/Nickel 201 Pipe and Fittings UNS N02201 2.4068
Alloy 200/Nickel 200 Pipe and Fittings UNS N02200 2.4066
ASTM A453 Grade 660 A/B/C/D Stainless Steel: Plate, Sheet, Bar, Rod, Forgings
Nickel Alloy INCOLOY 800HT Pipes and Fittings
Nickel Alloy Inconel 601 Pipes And Fittings
Nickel Alloy Monel 400 Pipes And Fittings
Nickel Alloy Incoloy 825 Pipes And Fittings
What is Nickel Alloy Pipe
Nickel alloy pipes are high-performance tubes made from nickel-based alloys (e.g., Inconel®, Monel®, Incoloy®, Nimonic®, Hastelloy®, Nickel®, Cu-Ni Alloy®, and High Nickel Alloys), designed for extreme conditions like high temperatures, corrosion, and pressure in industrial piping systems.
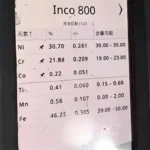
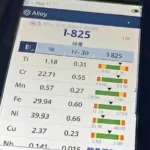
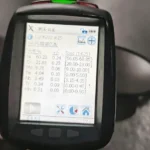
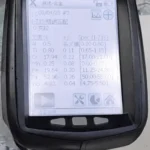
Nickel Alloy Pipes: Engineering Marvels for Extreme Industrial Environments
Nickel alloy pipes represent the pinnacle of metallurgical engineering, specifically engineered to withstand the most demanding operational conditions in modern industries. Composed of nickel-based alloys such as Inconel®, Monel®, Hastelloy®, and Cu-Ni alloys, these pipes excel in environments characterized by extreme temperatures (up to 1,200°C), corrosive media, and pressures exceeding 10,000 psi. Their unique chemical composition and advanced manufacturing processes make them indispensable in sectors ranging from aerospace to offshore energy.
Material Properties & Performance Advantages
Nickel alloy pipes derive their exceptional capabilities from precise elemental compositions. For instance:
- Nickel (40–70%): Enhances ductility and corrosion resistance.
- Chromium (15–23%): Forms a self-repairing oxide layer for high-temperature oxidation resistance.
- Molybdenum (2–16%): Provides pitting and crevice corrosion resistance in chloride-rich environments.
These alloys achieve superior performance metrics compared to conventional stainless steels (see Table 1).
Table 1: Nickel Alloy vs. Stainless Steel Performance Comparison
Property | Inconel® 625 | 316L Stainless Steel | Improvement |
---|---|---|---|
Max Operating Temp (°C) | 1,100 | 870 | +26% |
Corrosion Rate (mm/yr)* | 0.025 | 0.50 | 20x slower |
Tensile Strength (MPa) | 930 | 515 | +80% |
*In 10% HCl solution at 50°C |
Global Supply Chain Dynamics
The nickel alloy pipe market is dominated by specialized nickel alloy pipe manufacturers and suppliers who leverage proprietary technologies. Key players include:
- KCM Special Steel (China): Emerging nickel alloy pipe supplier producing cost-effective Pipes alternatives.
- Haynes International (US): Pioneer of Hastelloy® alloys, holding 22% of the aerospace-grade pipe market.
- Sandvik AB (Sweden): Supplies 35% of Europe’s nuclear reactor cooling systems with SANICRO® tubes.
Geopolitical factors significantly impact supply chains. For example, the 2022 LME nickel price surge (112% YoY) forced manufacturers to adopt innovative strategies, such as hybrid alloy designs with reduced nickel content (e.g., Incoloy® 825 with 38–46% Ni).
Critical Applications & Case Studies
1. Petrochemical Industry
Hastelloy® C-276 pipes are used in hydrocracker units, resisting sulfidic corrosion at 450°C. A 2023 ExxonMobil project reported a 40% lifespan extension compared to duplex stainless steel.
2. Aerospace Engineering
Nimonic® 263 alloy fuel lines in GE Aviation’s GEnx engines reduce weight by 18% while maintaining 1,050°C fatigue resistance.
3. Marine Systems
Cu-Ni 90/10 condensers in desalination plants demonstrate a corrosion rate of 0.03 mm/year in seawater, outperforming titanium in cost-efficiency.
Quality Standards & Certification
Reputable nickel alloy pipe manufacturers adhere to stringent certifications (Table 2), ensuring reliability across industries.
Table 2: Key Industry Certifications
Standard | Scope | Key Manufacturers Certified |
---|---|---|
ASTM B829 | Seamless pipe dimensional tolerances | Special Metals Corporation |
NACE MR0175 | Sulfide stress cracking resistance | Vallourec S.A. |
ASME SB622 | High-temperature service | Carpenter Technology |
Innovations by Leading Suppliers
Top nickel alloy pipe suppliers are driving technological advancements:
- Additive Manufacturing: DMG Mori’s laser-clad Inconel® 718 pipes achieve 99.98% density, reducing lead times by 60%.
- Smart Coatings: Bodycote’s Aluminized nickel alloy pipes increase oxidation resistance by 300% in thermal power plants.
- QC: We employs learning to detect sub-50μm defects in real-time production.
Market Trends & Forecast
The global nickel alloy pipe market is projected to grow at a 6.8% CAGR, reaching $38.2 billion by 2030 (Grand View Research, 2023). Key drivers include:
- Expansion of LNG infrastructure (32% demand surge anticipated by 2027).
- Adoption of Gen IV nuclear reactors requiring radiation-resistant alloys.
- Asia-Pacific dominance, with Chinese nickel alloy pipe suppliers capturing 28% of new contracts in 2023.
Challenges & Solutions
Challenge | Supplier/Manufacturer Response |
---|---|
Nickel price volatility | Long-term contracts with Indonesian miners |
Environmental regulations | Closed-loop recycling systems (85% scrap reuse) |
Counterfeit products | Blockchain-based material traceability |
Strategic Partnerships
Collaborations between nickel alloy pipe manufacturers and end-users are accelerating innovation. For example:
- Shell & Tata Steel’s $200M JV produces hyper-durable Monel® K-500 pipes for Arctic drilling.
- NASA partners with ATI to develop 3D-printed Inconel® 939 combustion chambers for Mars missions.
Conclusion
Nickel alloy pipes remain vital to industrial progress, with nickel alloy pipe suppliers and manufacturers continuously pushing material science boundaries. As industries face increasingly harsh operating conditions, the synergy between advanced alloys, smart manufacturing, and global supply chain resilience will define the next era of engineering excellence.
KCM Special Steel: Company Overview
KCM Special Steel Co., Ltd is a globally recognized nickel alloy pipe manufacturer headquartered in Zhejiang, China. With ISO 9001:2015 certification, KCM specializes in producing nickel-based alloy pipes tailored for high-temperature, high-pressure, and corrosive environments.
Key Highlights:
- Annual production capacity: 15,000 metric tons of nickel alloy pipes.
- Serving 50+ countries across oil & gas, chemical, power generation, and aerospace sectors.
- R&D-driven: 12% of revenue reinvested in material innovation and process optimization.
Product Portfolio: Nickel Alloy Pipes by KCMSS
KCM’s expertise spans a wide range of nickel alloys, each engineered for specific industrial challenges. Below is a summary of their core product lines:
Alloy Grade | Composition | Key Properties | Typical Applications |
---|---|---|---|
Inconel® 625 | Ni 58%, Cr 20%, Mo 9%, Nb 3.6% | Oxidation resistance (up to 980°C) | Aerospace exhausts, nuclear reactors |
Monel® 400 | Ni 67%, Cu 30%, Fe 1.5% | Seawater corrosion resistance | Offshore platforms, desalination plants |
Hastelloy® C-276 | Ni 57%, Mo 16%, Cr 16%, Fe 5% | Acid resistance (HCl, H₂SO₄) | Chemical reactors, pollution control |
Incoloy® 825 | Ni 42%, Fe 30%, Cr 21%, Mo 3% | Sulfidation resistance | Oil refining, sulfuric acid production |
Cu-Ni 90/10 | Cu 90%, Ni 10%, Fe 1% | Biofouling immunity, erosion resistance | Ship condensers, marine pipelines |
Manufacturing Capabilities
As a premier nickel alloy pipe supplier in China, KCM integrates cutting-edge technology with stringent quality controls to deliver precision-engineered solutions.
1. Advanced Production Processes
- Seamless Pipes:
- Produced via hot extrusion or cold drawing, ensuring uniform microstructure.
- Compliant with ASTM B163 (seamless) and ASTM B725 (welded).
- Welded Pipes:
- TIG (Tungsten Inert Gas) and laser welding for defect-free joints.
- Capable of diameters up to 1,200 mm and wall thicknesses up to 50 mm.
2. Quality Assurance Protocols
KCM’s ISO-certified nickel alloy pipe manufacturing process includes:
Stage | Testing Method | Standard | Acceptance Criteria |
---|---|---|---|
Material Verification | XRF (X-ray Fluorescence) | ASTM E1476 | Composition tolerance ≤ ±1% |
Mechanical Testing | Tensile, Hardness, Impact Tests | ASTM E8, ASTM E18, ASTM E23 | Yield strength ≥ 350 MPa |
Non-Destructive Testing | Ultrasonic Testing (UT) | ASME V, Article 4 | Zero inclusion defects > 0.5 mm |
Industry Applications and Case Studies
KCM’s nickel alloy pipes are trusted in mission-critical applications worldwide:
1. Oil & Gas: Subsea Pipeline Systems
- Client: Offshore drilling operator in the South China Sea.
- Solution: Monel® K500 pipes (OD 300 mm, WT 15 mm) for seawater cooling systems.
- Result: 20-year service life with zero corrosion failures.
2. Aerospace: Jet Engine Components
- Client: Global aerospace OEM.
- Solution: Inconel® 718 seamless pipes for turbine exhausts.
- Result: Withstood 10,000+ thermal cycles at 700°C.
3: Nickel 201 Pipe in Chemical Processing
Client: A European chemical plant specializing in caustic soda production.
Challenge: Corrosion resistance in high-temperature alkaline environments (pH >14).
Solution: KCM Special Steel supplied Nickel 201 pipes (OD 150 mm, WT 10 mm) with seamless construction and pickled surface finish. The alloy’s low carbon content (<0.02%) minimized carbide precipitation during prolonged exposure to 400°C conditions.
Result:
- Service life extended by 35% compared to stainless steel alternatives.
- Zero maintenance downtime over 5 years of operation.
4: Incoloy 800H Pipe for Petrochemical Furnaces
Client: Middle Eastern refinery upgrading pyrolysis furnace tubing.
Challenge: Creep resistance at 750°C under cyclic thermal stress.
Solution: KCM provided Incoloy 800HT pipes (ASTM B407) with 0.06–0.10% carbon content, enhancing high-temperature strength. Custom dimensions (OD 200 mm, WT 12 mm) accommodated complex furnace layouts.
Result:
- Sustained 15,000 operating hours without deformation.
- Reduced unplanned shutdowns by 50%.
5: Inconel 625 Pipe in Offshore Gas Compression
Client: North Sea offshore platform managing sour gas (H₂S-rich) pipelines.
Challenge: Resistance to sulfide stress cracking (SSC) and chloride pitting.
Solution: Inconel 625 seamless pipes (NACE MR0175 compliant) with 58% nickel and 9% molybdenum content were deployed. KCM’s cold-worked tubing achieved yield strength >550 MPa.
Result:
- No SSC incidents reported over 8 years.
- Reduced inspection frequency by 30%.
6: Hastelloy C276 Pipe for Flue Gas Desulfurization
Client: Chinese power plant retrofitting scrubber systems.
Challenge: Corrosion in sulfuric acid (pH 2–3) and chloride-laden environments.
Solution: Hastelloy C276 welded pipes (ASTM B619) with Mo 16% and Cr 15% provided immunity to localized attack. KCM’s TIG-welded joints passed 100% radiographic testing.
Result:
- Scrubber lifespan increased from 3 to 12 years.
- Annual maintenance costs reduced by $1.2 million.
7: Alloy 20 Pipe in Pharmaceutical Reactors
Client: U.S.-based pharmaceutical manufacturer requiring nitric acid resistance.
Challenge: Stress corrosion cracking (SCC) in 65% HNO₃ at 80°C.
Solution: KCM delivered Alloy 20 pipes (UNS N08020) stabilized with niobium to prevent sensitization. Custom lengths (6 m) minimized weld points in reactor assemblies.
Result:
- Eliminated SCC failures across 10 reactor vessels.
- Achieved FDA-compliant material traceability.
8: Hastelloy C22 Pipe for Waste Incineration
Client: German waste-to-energy plant handling halogenated compounds.
Challenge: Oxidation resistance in 950°C flue gases containing HCl and Cl₂.
Solution: Hastelloy C22 seamless pipes (ASTM B622) with 56% Ni and 13% Mo resisted aggressive ash deposits. KCM’s solution included post-weld heat treatment (PWHT) to restore ductility.
Result:
- Operational temperature capability increased by 150°C.
- Maintenance intervals extended from 6 to 18 months.
9: Alloy 28 Pipe in Seawater Desalination
Client: Saudi Arabian desalination plant combating biofouling and crevice corrosion.
Challenge: Long-term durability in seawater (40,000 ppm Cl⁻) at 60°C.
Solution: Alloy 28 (UNS N08028) pipes with 3% Cu and 31% Ni provided superior pitting resistance. KCM’s electropolished surface finish (Ra <0.8 µm) minimized microbial adhesion.
Result:
- 25-year design life validated by accelerated testing.
- Energy consumption reduced by 12% due to smoother fluid flow.
10: Alloy 31 Pipe for Sulfuric Acid Storage
Client: Chilean copper mining company storing 98% H₂SO₄.
Challenge: Uniform corrosion rates <0.1 mm/year in concentrated acid.
Solution: Alloy 31 pipes (UNS N08031) with 6.5% Mo and 1.2% Cu delivered exceptional corrosion resistance. KCM’s seamless manufacturing avoided weak points in welded joints.
Result:
- Achieved corrosion rate of 0.05 mm/year.
- Storage tank replacement cycle extended from 5 to 15 years.
Technical Comparison of Key Nickel Alloys
Alloy | Key Composition | Max Temp (°C) | Primary Industry Use |
---|---|---|---|
Nickel 201 | Ni 99%, C 0.02% | 600 | Chemical processing |
Incoloy 800H | Ni 32%, Cr 21%, Fe 39% | 750 | Petrochemical furnaces |
Hastelloy C276 | Ni 57%, Mo 16%, Cr 16% | 400 (acidic) | Pollution control systems |
Alloy 31 | Ni 31%, Mo 6.5%, Cu 1.2% | 450 | Sulfuric acid storage |
Why Partner with KCM Special Steel?
As a leading nickel alloy pipe supplier and nickel alloy pipe manufacturer, KCM combines:
- Material Expertise: Over 50 alloy grades tailored for extreme conditions.
- Certified Quality: ISO 9001, TPI, and NACE compliance.
- Global Support: Lage quantity in stock (China) 0ensure rapid delivery.
Why Choose KCM as Your Nickel Alloy Pipe Supplier?
- End-to-End Customization:
- Tailored dimensions, heat treatments, and surface finishes (e.g., pickled, polished).
- Global Logistics Network:
- Large Quantity Nickel Alloy Pipes in Stock ensure timely delivery.
- Technical Expertise:
- In-house metallurgists and engineers provide application-specific guidance.
Sustainability and Innovation
KCMSS prioritizes eco-friendly practices:
- Recycled Content: 30% of raw materials sourced from nickel scrap.
- Energy Efficiency: Solar-powered facilities reduce carbon footprint by 25%.
FAQ: Nickel Alloy Pipes – Suppliers, Manufacturers, and Key Considerations
1. What are nickel alloy pipes, and why are they preferred in extreme environments?
Nickel alloy pipes are high-performance tubing made from nickel-based alloys (e.g., Inconel®, Monel®, Hastelloy®), engineered to withstand extreme temperatures, corrosive chemicals, and high-pressure conditions. Their superior heat resistance, corrosion immunity, and mechanical durability make them indispensable in industries like oil & gas, aerospace, and chemical processing. Reputable nickel alloy pipe suppliers and nickel alloy pipe manufacturers ensure these pipes meet stringent performance standards.
2. How do I choose a reliable nickel alloy pipe supplier?
Look for:
- Certifications: ISO 9001, API, and ASME compliance (e.g., nickel alloy pipe manufacturer in China KCM Special Steel holds ISO 9001:2015).
- Material Expertise: Ability to produce alloys like Incoloy® 825 or Hastelloy® C-276.
- Customization: Options for tailored dimensions, coatings, and testing protocols.
- Global Reach: Suppliers with logistics hubs in strategic locations (e.g., China, Europe, North America).
3. Why source from a China nickel alloy pipe supplier?
China-based manufacturers like KCM Special Steel offer:
- Cost Efficiency: Competitive pricing due to advanced production infrastructure.
- Scale: High-volume production (e.g., 15,000+ metric tons annually).
- Quality: Compliance with ASTM, DIN, and EN standards.
- Innovation: R&D investment in high-entropy alloys (HEAs) and additive manufacturing.
4. What certifications should a nickel alloy pipe manufacturer have?
Key certifications include:
- ISO 9001: Quality management systems.
- ISO 14001: Environmental management.
- API 5LC/5LD: Standards for corrosion-resistant alloy pipelines.
- NACE MR0175: Resistance to sulfide stress cracking.
Always verify certifications when engaging a nickel alloy pipe manufacturer in China or globally.
5. Can nickel alloy pipes be customized for specific applications?
Yes. Leading nickel alloy pipe suppliers provide:
- Tailored Dimensions: Custom outer diameters (OD), wall thicknesses (WT), and lengths.
- Surface Finishes: Polished, pickled, or sandblasted surfaces.
- Heat Treatments: Annealing, quenching, or aging to enhance properties.
- Testing: Third-party mechanical, chemical, and NDT reports.
6. What industries rely on nickel alloy pipe manufacturers?
Major sectors include:
- Oil & Gas: Subsea pipelines (Monel® 400), sour gas handling (Incoloy® 925).
- Aerospace: Jet engine exhausts (Inconel® 625), fuel systems (Nimonic® 90).
- Chemical Processing: Acid transport (Hastelloy® C-276), reactor vessels (Nickel 201).
- Power Generation: Nuclear coolant systems (Inconel® 690).
7. How do China-based suppliers ensure quality control?
Top China nickel alloy pipe suppliers implement:
- Spectrometry Testing: XRF (X-ray fluorescence) for precise composition analysis.
- NDT Methods: Ultrasonic testing (UT) and radiography for defect detection.
- Mechanical Tests: Tensile strength, hardness, and impact testing per ASTM standards.
- Traceability: Mill test reports (MTRs) for every batch.
8. What is the typical lead time for orders from a nickel alloy pipe manufacturer?
Lead times vary by complexity:
- Standard Sizes: 4–6 weeks for seamless/welded pipes.
- Custom Orders: 8–12 weeks for exotic alloys or special coatings.
Suppliers like KCM Special Steel optimize lead times via vertically integrated production.
9. How do nickel alloy pipes compare to stainless steel or carbon steel pipes?
Property | Nickel Alloys | Stainless Steel | Carbon Steel |
---|---|---|---|
Temperature Resistance | Up to 1,200°C | Up to 800°C | Up to 450°C |
Corrosion Resistance | Excellent (acid, seawater) | Moderate (oxidizing environments) | Poor (requires coatings) |
Cost | Higher | Moderate | Low |
10. Are nickel alloy pipes environmentally sustainable?
Yes. Leading nickel alloy pipe manufacturers prioritize sustainability by:
- Recycling: Nickel alloys are 100% recyclable without property loss.
- Energy Efficiency: Solar-powered factories (e.g., KCM reduces CO₂ by 25%).
- Waste Reduction: Additive manufacturing minimizes material waste.
11. How do I verify the credibility of a nickel alloy pipe supplier in China?
- Check certifications (ISO, TPI).
- Review case studies or client testimonials (e.g., offshore oil projects).
- Request samples and third-party test reports.
- Evaluate responsiveness and technical support.
12. Can I get technical support from a nickel alloy pipe manufacturer?
Reputable suppliers like KCM Special Steel offer:
- Material Selection Guidance: Matching alloys to operational conditions.
- Failure Analysis: Diagnosing field issues (e.g., corrosion, fatigue).
- CAD/Design Support: Optimizing pipe geometries for efficiency.
Conclusion
As a leading nickel alloy pipe supplier in China and ISO-certified manufacturer, KCM Special Steel Co., Ltd combines technological excellence with unwavering quality. Their commitment to innovation, sustainability, and customer-centric solutions makes them the partner of choice for industries pushing the boundaries of performance. For projects demanding reliability under extreme conditions, trust KCM to deliver pipes that power progress.
Contact KCM Special Steel:
- Website: www.duplexstainlesssteelpipes.com
- Email: kcmspecialsteel@outlook.com
- Tel: +86-13758498349
- Whatsapp:+86-13758498349