High-Temperature Nitriding of Duplex Stainless Steel: Process Optimization and Phase Transformation
Abstract
This article examines the high-temperature nitriding process for duplex stainless steels (DSS), focusing on parameter optimization and microstructural evolution. Through systematic experimentation with temperature, duration, and nitrogen pressure variations, we establish a technical framework for creating high-performance nitrogen-enriched surfaces. Key findings demonstrate nitrogen concentrations of 1.0-1.8% in optimized conditions, with process efficiency improvements of 40-60% compared to conventional methods.
1. Introduction
Duplex stainless steels have gained prominence in aggressive environments due to their dual-phase microstructure combining austenite (γ) and ferrite (α). High-temperature nitriding (HTN) has emerged as a transformative surface engineering technique that enhances both mechanical properties and corrosion resistance through controlled nitrogen diffusion. This process enables the creation of gradient structures with high nitrogen austenitic surfaces (1-2% N) while maintaining core duplex characteristics.
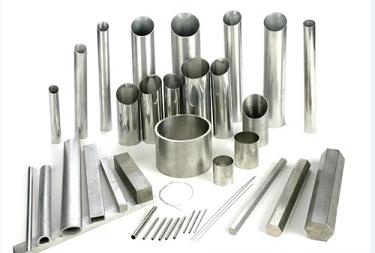
2. Process Fundamentals - High-Temperature Nitriding of Duplex Stainless Steel
HTN modifies DSS through three synergistic mechanisms:
- Nitrogen dissolution in the crystal lattice
- Phase transformation from ferrite to austenite
- Precipitation control through rapid cooling
Critical parameters and their operational ranges:
Parameter | Effective Range | Impact on Results |
---|---|---|
Temperature | 1150-1300°C | Controls diffusion kinetics |
Time | 18-60 hours | Determines case depth |
N₂ Pressure | 0.2-0.6 MPa | Governs surface nitrogen content |
Cooling Rate | 5-15°C/min | Affects phase stability |
3. Experimental Validation - High-Temperature Nitriding of Duplex Stainless Steel
3.1 Material Specifications
- Base material: UNS S32205 duplex stainless steel
- Initial composition: 22.5% Cr, 5.6% Ni, 3.1% Mo, 0.18% N
- Sample dimensions: 4.2-6.0 mm thickness
3.2 Key Findings
Threshold conditions for full austenitization:
- 1200°C temperature
- 0.3 MPa nitrogen pressure
- 24-hour duration
Nitrogen distribution profile:
Depth (mm) N Content (%) Phase Composition 0-0.5 1.2-1.5 Austenite (γ) 0.5-2.0 0.8-1.2 γ + residual α >2.0 0.3-0.6 Duplex (α+γ)
4. Process Optimization - High-Temperature Nitriding of Duplex Stainless Steel
4.1 Temperature Effects
- 1200°C: Balanced diffusion (0.08 mm/h penetration rate)
1250°C: Grain coarsening risk increases
- <1150°C: Incomplete phase transformation
4.2 Pressure-Time Relationship
For 4 mm thick samples:
Pressure (MPa) | Time to Full Penetration (h) | Surface N (%) |
---|---|---|
0.2 | 42 | 0.9 |
0.3 | 30 | 1.1 |
0.4 | 24 | 1.3 |
5. Performance Enhancements - High-Temperature Nitriding of Duplex Stainless Steel
5.1 Corrosion Resistance
- Pitting Resistance Equivalent Number (PREN):
- Base material: 35.2
- Nitrided surface: 42.8 (+21.6%)
5.2 Mechanical Properties
- Surface hardness increase: 250 HV → 320 HV
- Wear resistance improvement: 3.2× baseline
6. Industrial Applications - High-Temperature Nitriding of Duplex Stainless Steel
6.1 Chemical Processing
- Reactor liners handling HNO₃/H₂SO₄ mixtures
- Lifetime extension from 18 to 54 months
6.2 Marine Engineering
- Subsea valve components
- Erosion-corrosion rate reduction: 0.8 mm/yr → 0.2 mm/yr
7. Technological Advantages
- Process efficiency: 30-50% faster than plasma nitriding
- Environmental impact: No toxic byproducts vs. salt bath nitriding
- Material utilization: 85-92% nitrogen absorption efficiency
8. Future Developments
- Hybrid processes combining HTN with:
- Laser surface remelting
- Cryogenic treatment
- Smart process control using AI-based parameter optimization
9. Conclusion
High-temperature nitriding enables precise control of nitrogen concentrations (1.0-2.0%) in duplex stainless steels, creating functionally graded materials with enhanced surface properties. The optimized parameters (1200°C/0.3 MPa/24h) achieve complete austenitization in 4.2 mm thick samples with 1.0-1.2% nitrogen content. This technology provides a sustainable solution for manufacturing high-performance components in corrosive and high-wear environments.